The Basics of Polyimide|
An Explanation of how it is Used
2021/12/17
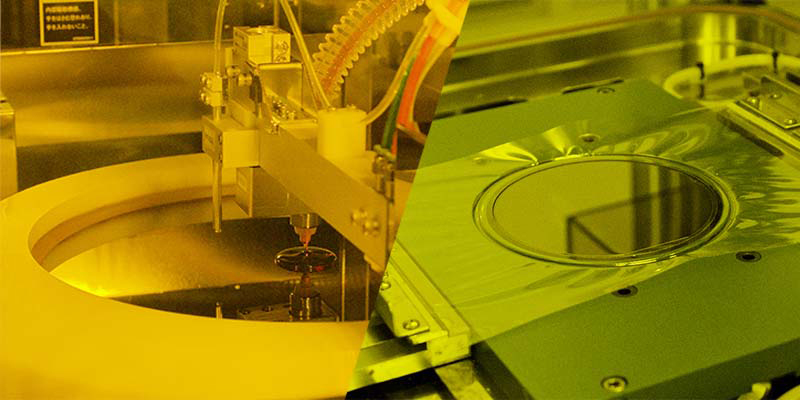
- <Table of Contents>
- ●The Basics of Polyimide
- ●Properties of Polyimide
- ●Polyimide applications
- ●Toray Polyimide Products
The Basics of Polyimide
Polyimide (abbreviated as PI) is a polymer compound with an imide ring bond (Fig. 1) in its molecular chain. Aromatic polyimides, in which this “R” is aromatic, are widely used in industry.
Fig. 1
Due to PI’s stabilized physical properties between 196°C and 300°C, extreme heat resistance, robust mechanical properties, excellent dielectric properties and chemical resistance, it is widely used in aerospace, automotive and consumer products.
The composition of polyimide is shown in Figure 2. First, two dry compounds of diamine and carboxylic anhydride are combined for the purpose of creating polyamic acid (polyamide acid), which is highly soluble in organic solvents. Then when polyamic acid is cured at high temperature, it goes through imidization (dehydration and cyclization), finally becoming polyimide.
Fig. 2
Polyimides are generally categorized as either thermosetting or thermoplastic.
Thermosetting polyimide has a high glass transition temperature (Tg) and it is widely used for coatings and film substrates. Thermoplastic polyimides have Tg between 200 and 300°C. Thermal plastics can easily be molded into different shapes; therefore, they are used for various parts of the machinery in many industries.
Properties of Polyimide
Excellent features and characteristics of PI:
- (1) Excellent heat resistance and very high tensile strength at high temperatures.
- (2) Electrical properties (dielectric constant, volumetric resistance, etc.) remain virtually unchanged from cryogenic to high temperatures.
- (3) It has very high heat resistance of 450°C or higher.
- (4) It exhibits little thermal expansion due to its low coefficient of thermal expansion, giving it high dimensional stability.
- (5) High thermal conductivity.
- (6) It offers excellent flame resistance and is less flammable than other polymer resins (such as polyester).
It does not dissolve in most organic solvents, and exhibits good chemical resistance even at high temperature.
Polyimide applications
Due to PI’s excellent mechanical properties, it has been used for various applications.
Polyimide is widely used in electronic devices such as flexible printed circuits (FPCs), especially within smartphones and automobiles. Furthermore, PI is used for motor coils, wire coating, and dielectric/passivation layer(s) for semiconductors.
In displays, polyimide is used for the alignment of the liquid crystal molecules in a specific LCD orientation, and it is also used as a pixel-separating film in organic EL displays.
With PI’s rigidness, robustness, thickness precision and low outgas, it is also used for cutting processes for semiconductor and automobile manufacturing equipment.
Furthermore, in the field of aerospace, its high heat resistance and electrical insulation property allow PI to be used for the protective passivation film for critical satellite devices.
Toray Polyimide Products
After launching the heat-resistant insulating varnish TORAYNEECE™ in 1970, Toray introduced non-photodefinable polyimide varnish, SEMICOFINE™, to the market in 1979. After its introduction, SEMICOFINE™ became a crucial part of the protective and insulating films for semiconductor devices. In 1985, in order to utilize the polyimide varnish efficiently, PHOTONEECE™, a photodefinable polyimide varnish, was developed. Toray currently offers a wide range of product grades, both in varnish and B-stage film (FALDA™). These non-photodefinable and photodefinable products are used in the fields of semiconductors, electronic components, and mounting.
Furthermore, narrow-pitch, flexible circuit substrates made with our fine patterning technology are also used in various types of displays.
The following are some of the main applications utilizing Toray products.
- Buffer Coatings: SEMICOFINE™ and PHOTONEECE™
- Polyimide, having excellent flexibility, adhesion and heat resistance, is used for the purpose of preventing cracking and misalignment of wiring caused by differences in thermal expansion coefficients between the mold resin and the mounted semiconductor chips.
- Redistribution Layer: SEMICOFINE™ and PHOTONEEC™
- Miniaturization and multi-layered semiconductor packages require insulating materials that possess high photo resolution with robust mechanical properties. Fan-Out Wafer Level Packaging (FO-WLP), in particular, requires low-temperature curing material with adhesion to Cu.
- Cavity Structure Materials: FALDA™
- The use of electronic components with cavity structures, such as MEMS sensors and RF devices, is increasing in smartphones and automobiles. With its excellent mechanical properties, polyimide is used for cavity structure materials. With FALDA’s high modulus elasticity, B-stage polyimide film is well-suited for forming cavity structures.
- Materials for Flexible Printed Circuit Boards: Single-sided COF and Doubled-sided COF
- Evolving needs of high definition displays require miniaturization of wiring on mounted driver ICs’ flexible printed circuit boards on COF (Chip On Film) technologies. In addition, by forming circuits on both sides of the film, circuits will become multi-layered and further miniaturizations will be possible.